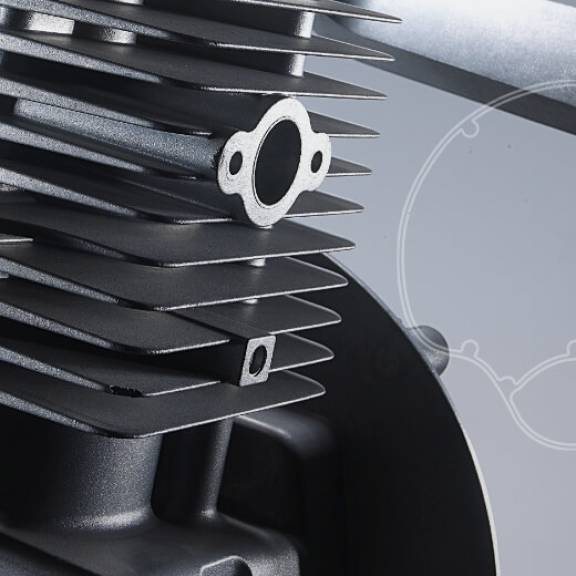
Produzione innovazione
/Production
A single reference partner
Normalien is a reference partner for the development of new projects: from prototyping until the finished product, ready for pass-free delivery to the final customer.
The production department, the nerve centre of the company, is equipped with fully automated and robotised die casting cells, from 500 to 3.000 tons, capable of producing parts ranging from 100 g up to 60 kg.
The production department, the nerve centre of the company, is equipped with fully automated and robotised die casting cells, from 500 to 3.000 tons, capable of producing parts ranging from 100 g up to 60 kg.
A more complex casting
to optimize the assembly process
by the final customer
to optimize the assembly process
by the final customer
01/Co-design
A synergistic design
Each project is developed by a Team of experienced technicians, combining the know-how gained in 50 years of experience and the most advanced technologies, including design software and 3D simulations.Co-design phases:
• Design concept: product requirements and functional analysis, modelling, optimization of die-cast components based on the final assembly demands
• Casting process analysis: vacuum and squeeze pin development, casting simulation, design of 3D-CAD casting shot (CATIA, PRO-ENGINEER), construction of 3D-CAD mould design.
• Manufacturing of the soft tooling, prototyping and serial moulds
• Quality Management – FMEA, APQP, PPAP
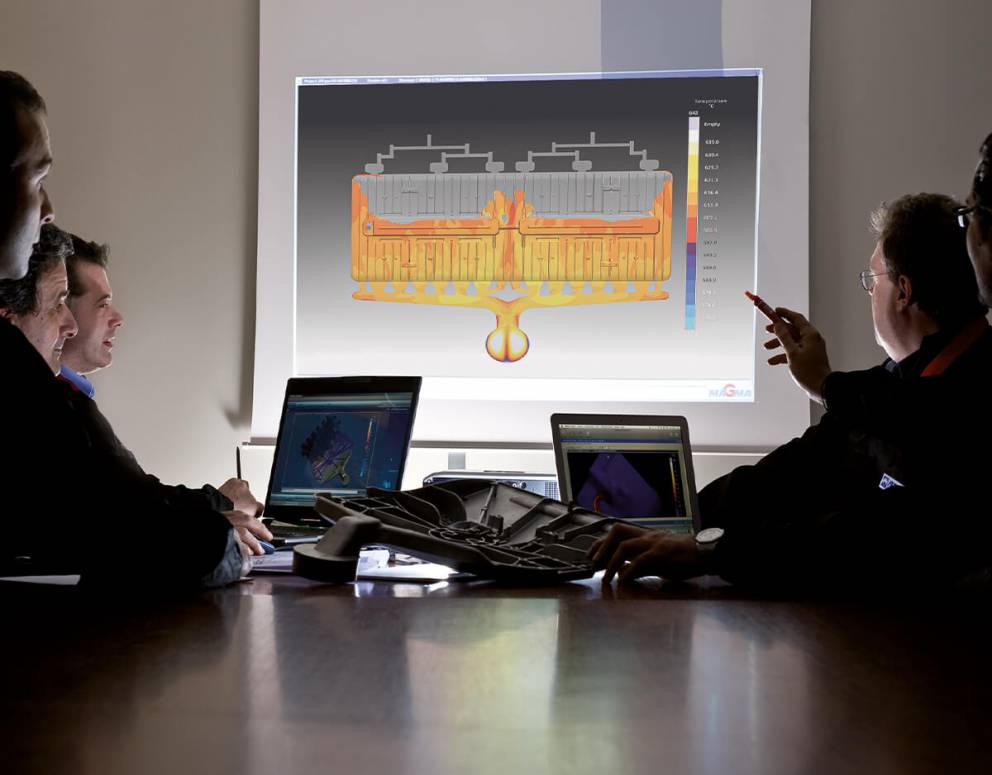

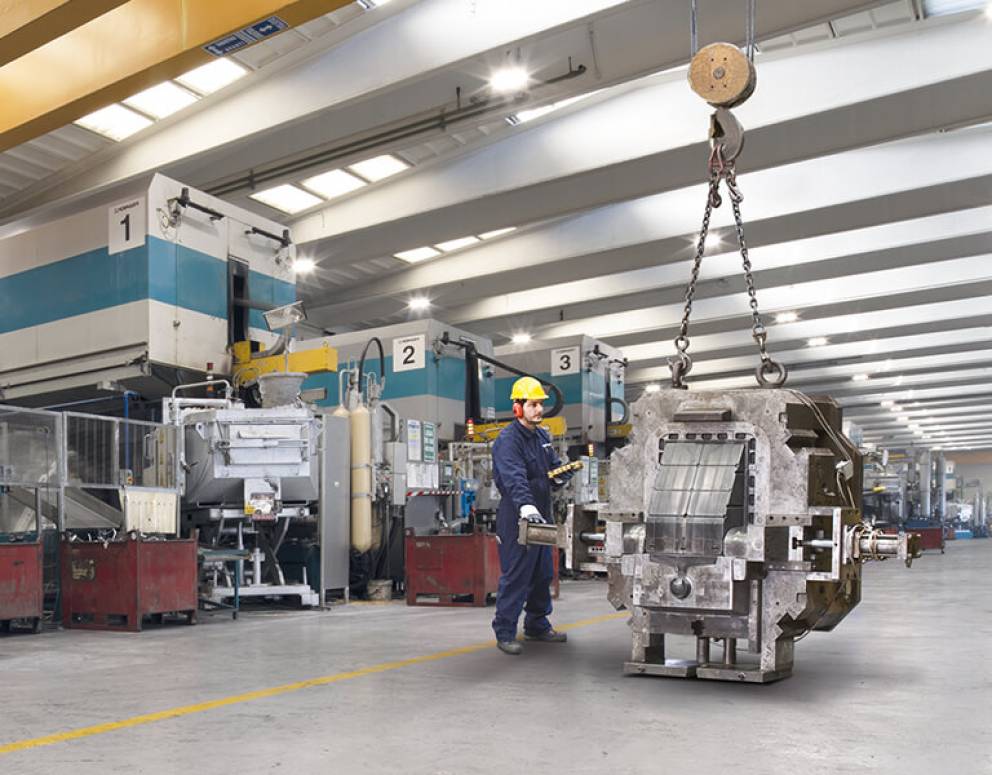
03/Die-casting
Lean Production
The foundry is equipped with casting cells: Bühler DCMs from 500 to 3000 tons, fully automated with multiple robots, Wollin lubricating systems, mould temperature control units, Striko Westofen electric holding furnaces, trimming presses and deburrig devices on-board.The critical characteristics of each component are handled with specific technologies, such as Squeeze-pin, Vacuum Fondarex, and Spot cooling systems.
In recent years, the foundry has evolved from the traditional die-casting machine to the new “complete cell” concept, where multiple processes suchas die-casting, trimming, deburring and shotblasting are incorporated into the Lean Production concept.
Towards the final product, through a customized finishing line
Normalien has a specific corporate know-how for the treatment of surface finishing, that enables to process both aesthetical and high standard technology components, securing the highest quality level. Our line is equipped with Automatic grinding plants for a flexible process in-house, which ensures a smooth and stable surface finishing for the entire product lifetime.
Shotblasting and Grinding prepare the surface for the next treatments, all managed by Normalien as a single reference partner: powder coating, CED painting, tampo printing.
Shotblasting and Grinding prepare the surface for the next treatments, all managed by Normalien as a single reference partner: powder coating, CED painting, tampo printing.
04/Surface finishing
Maximum customization
Normalien has a specific corporate know-how for the treatment of surface finishing, that enables to process both aesthetical and high standard technology components. Our line is equipped with Automatic grinding plants for a flexible process in-house, which ensures a smooth and stable surface finishing for the entire product lifetime.Shotblasting and Grinding prepare the surface for the next treatments, all managed by Normalien as a single reference partner: powder coating, CED painting, tampo printing.
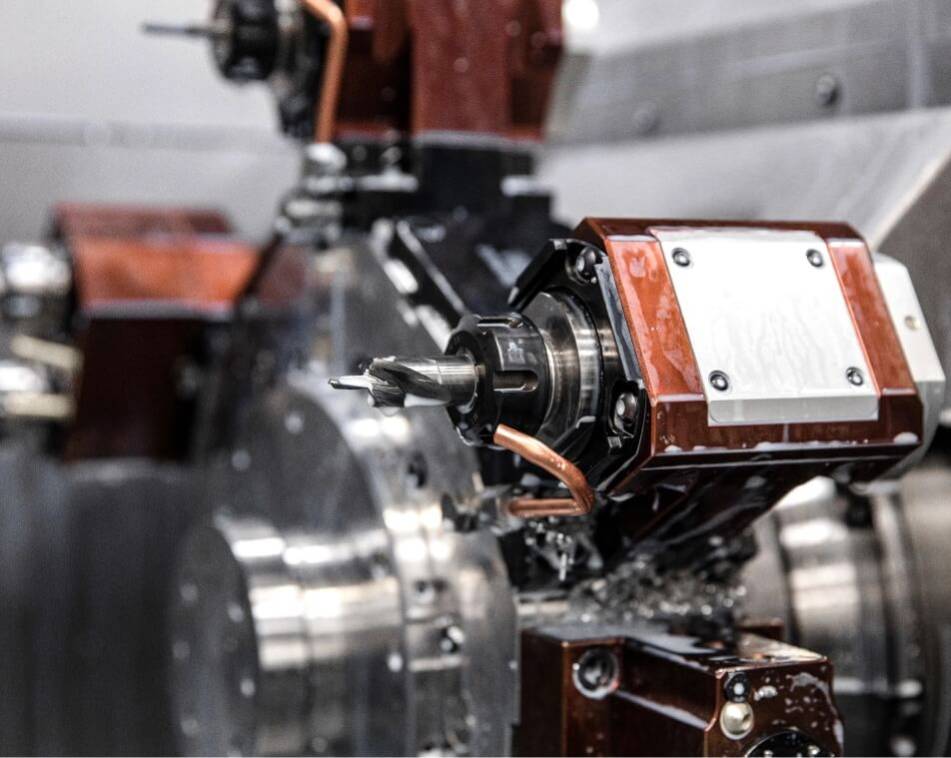
The mechanical machining department is equipped with high-precision machining centres, capable to machine
components up to 30 kg.
In particular, we have:
• Okuma lathes
• EMAG vertical lathes
• Mori Seiki horizontal machining centres
• MAZAK vertical processing centres
The processing lines are equipped with specialised washing systems and ZEISS machines for threedimensional checks integrated directly into the line.
components up to 30 kg.
In particular, we have:
• Okuma lathes
• EMAG vertical lathes
• Mori Seiki horizontal machining centres
• MAZAK vertical processing centres
The processing lines are equipped with specialised washing systems and ZEISS machines for threedimensional checks integrated directly into the line.
05/Mechanical machining
Key processes at Zero Mile
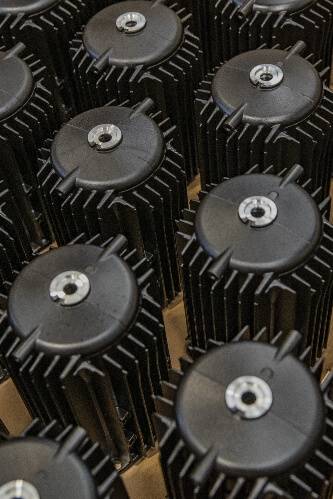
06/Foamed gaskets
Silicone and polyurethane gasket
A fully automated system, equipped with double robots for loading and unloading, as well as with a specific vision system, is carefully dosing either silicone PUR gaskets directly on the components, as a further step which is completing the service to the final Customer.
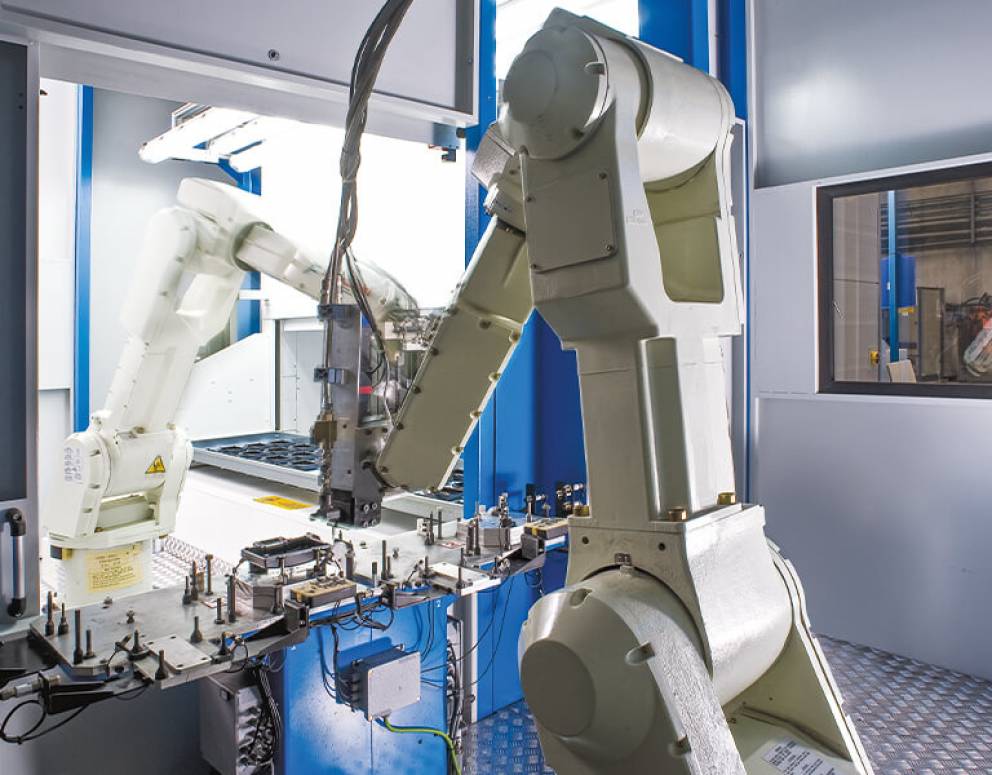
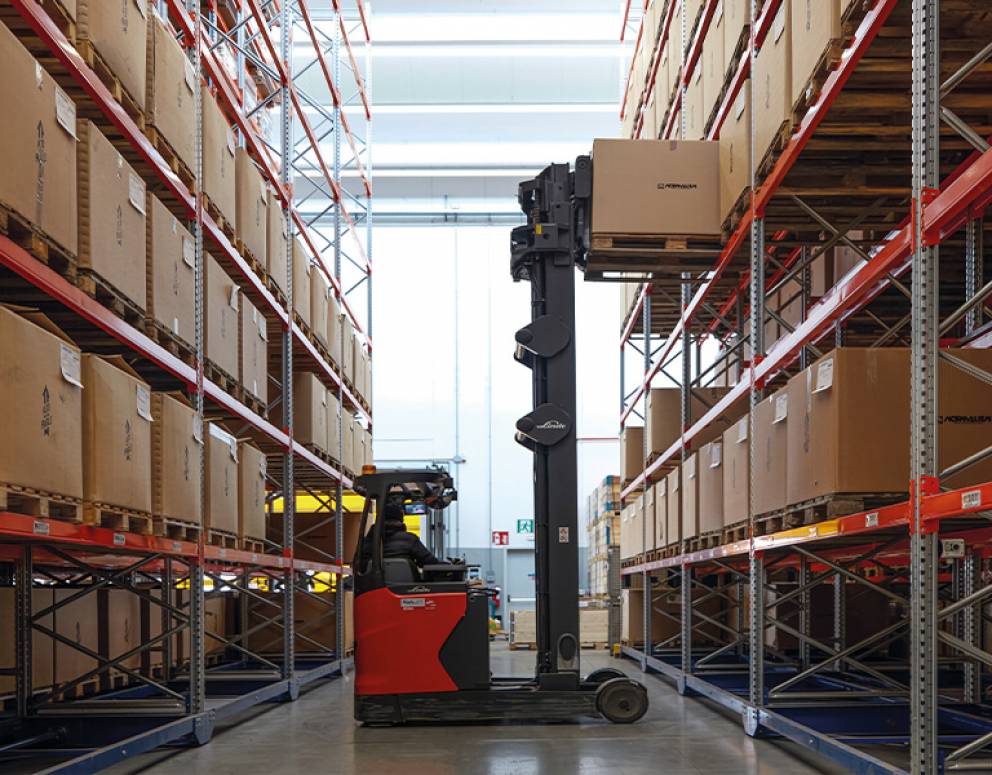
07/
Warehouse
Automated vertical storage
Normalien can offer its customers security stocks with additional capacity of 4.000 pallets for finished product, thanks to its new automated vertical storage.Our system ensures:
• Automatic location identification
• Instant 3D stock overview
• Optimization of space
• Cost-saving management of unloading/loading times
• Work safety
• Barcode system for traceability